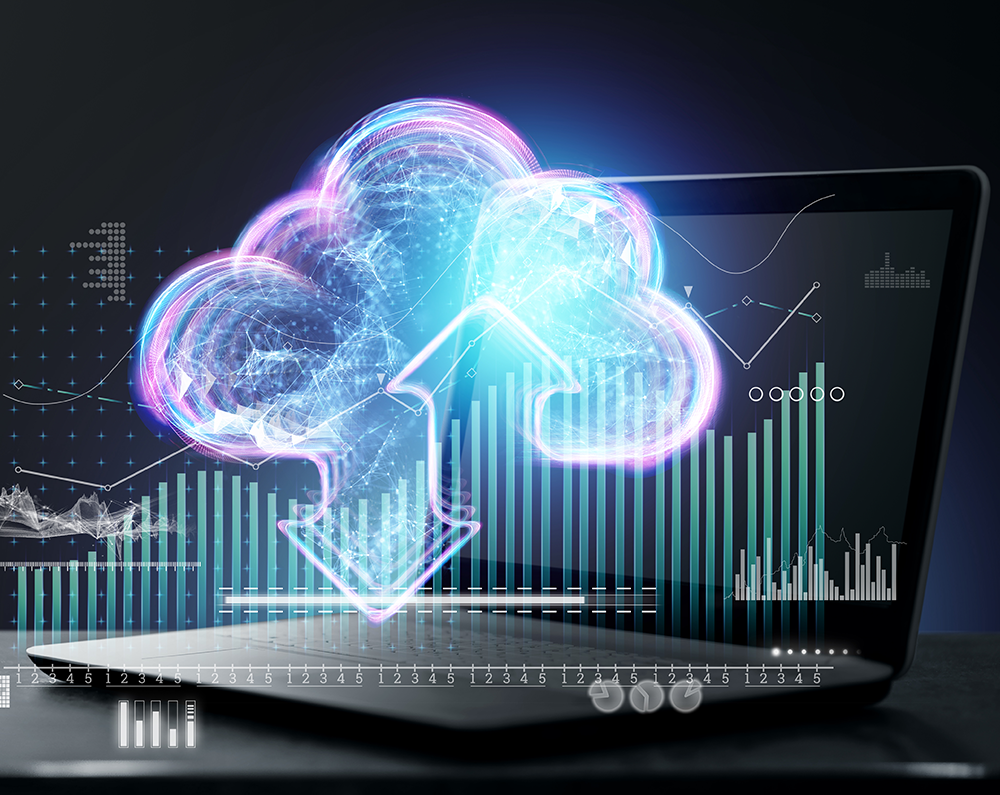
Microsoft Fabric and Reporting Cloud
Leverage Microsoft Fabric with our Reporting Cloud for real-time analytics, AI-powered insights, and seamless integration across platforms.
#DrivingExpertLedTransformation
KORCOMPTENZ is a Microsoft Gold-Certified Partner headquartered in New Jersey with extensive experience improving business outcomes for our customers. We leverage end-to-end solutions involving the ongoing convergence of ERP, Azure Cloud, Analytics, Artificial Intelligence, and IoT. We specialize in the Microsoft Dynamic 365 range of products such as Dynamics 365 Business Central, Dynamics 365 Finance and Operations, and Dynamics 365 CRM. Request a consultation today!
Leverage Microsoft Fabric with our Reporting Cloud for real-time analytics, AI-powered insights, and seamless integration across platforms.
Explore what Microsoft Dynamics 365 is, how it works, and what it’s used for. Discover its CRM & ERP capabilities, benefits, and features with Korcomptenz, your trusted Dynamics 365 partner.
Microsoft Power BI with Dynamics 365 products can provide valuable data insights and support for your sales team to make informed decisions.
Cookie | Duration | Description |
---|---|---|
cookielawinfo-checkbox-analytics | 11 months | This cookie is set by GDPR Cookie Consent plugin. The cookie is used to store the user consent for the cookies in the category "Analytics". |
cookielawinfo-checkbox-functional | 11 months | The cookie is set by GDPR cookie consent to record the user consent for the cookies in the category "Functional". |
cookielawinfo-checkbox-necessary | 11 months | This cookie is set by GDPR Cookie Consent plugin. The cookies is used to store the user consent for the cookies in the category "Necessary". |
cookielawinfo-checkbox-others | 11 months | This cookie is set by GDPR Cookie Consent plugin. The cookie is used to store the user consent for the cookies in the category "Other. |
cookielawinfo-checkbox-performance | 11 months | This cookie is set by GDPR Cookie Consent plugin. The cookie is used to store the user consent for the cookies in the category "Performance". |
viewed_cookie_policy | 11 months | The cookie is set by the GDPR Cookie Consent plugin and is used to store whether or not user has consented to the use of cookies. It does not store any personal data. |